Battery manufacture appears to be more of a craft than
a precise engineering science.
Take lead acid battery plate pasting for example. At 5 ELBC,
the Editor Gerry Wolf (GW) met with Giovanni Terzaghi (GT)
of Termar to learn something about belt pasting.
This reported dialogue is an account of that meeting.
GW: Our Let's Learn series said it all really.
Improve on quality, composition of raw materials,
their formulation, the training of staff and testing
of product and you can make a better battery that
lasts longer. So where does pasting fit into that
equation?
|
GT: A silent
revolution occurred in the pasting process by the introduction
of seamless belts for automatic pasting machines. The
electrical characteristics and life of lead storage
batteries depend gretly on the structure and phases
present in the active material which, in turn, result
from the composition and properties of the pastes.
To enable plates to deliver their rated capacity in
batteries, plates must be pasted with weight of paste
in the weight range specified.
The paste applying operation is the process during which
the properly mixed paste is applied to grid panels of
the proper composition and stiffness. The pasting belt
plays an important role in this process.
Control of the weight, thickness and density of the
resulting pasted plate will determine process ability
of the plate in the battery assembling area. All of
these characteristics combine to determine how the plate
will perform in the finished battery. |
GW: So what are the advantages of belt pasters
versus the competitive systems (fixed orifice, continuous
pasting with steel belts, extruding pasters, etc)and
why is belt pasting still so popular? |
GT: The belts
pasters are a more forgiving type of system than say,
the fixed orifice or steel belt pasters. The tolerances
of casting a grid do not need to be held as close, because
the belt will give a little when the thickness of the
plate is on the high side.
The need for operator skills are not as high or demanding
with a belt paster as with some of the other types of
machines. The overhead costs for a belt paster are not
as high as fixed orifice or continuous cast lines.
On some systems you have to soften or add water to the
mix to paste the plate but with a belt paster this is
not required. |
GW: And what are the shortcomings of belt pasters? |
GT: The only
shortcoming I see with a belt paster is that you have
to change the belts on a regular basis |
GW:
How can belt pasters be improved? Better running,
better operating practice? And how much difference
does the belt material make?
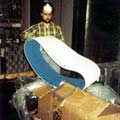
|
GT: Obviously
you have to employ a good preventative maintenance
programme to keep the machine running as it was designed
to run. Secondly changing from traditional cotton
belts to Industrie Tessili Bresciane (I.T.B.) seamless
belts will certainly improve the paster's performance,
and as you can see for yourself, I've got customer
endorsement to that effect.
I.T.B. seamless pasting machine belts have been developed
in close cooperation with battery makers, taking into
consideration all the problems connected with the
pasting process. Pasting machine manufacturers and
pasting process engineers pointed out the following
problems and requirements to design an ideal belt:
- Traditional pasting belts are woven open-ended.
The two fabric ends are then sewn and glued to get
a ring shaped belt. They have therefore a weaker
seam zone.
- The belt must have the same strength in all its
points while traditional cotton belts may have a
seam break zone.
- The belt must have the same thickness and surface
smoothness throughout its circumference to give
a better pasting and improved active material distribution
on battery grids.
- Water absorption must be uniform in every point.
No glue should be used for seam purposes in the
belt.
- The belt must run straight on the pasting machines
and not move towards one side or another. It must
be perfectly cylindrical. The belt should be dimensionally
stable to avoid textile structure distortions. The
belt life time should be extended as much as possible
to reduce the amount of down time on the pasting
lines to replace the belts.
|
GW:
So when did you produce the first seamless belt?
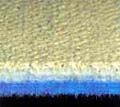
|
GT: About
fifteen years ago, I.T.B. and Termar technicians recognised
the need for an improved product to replace the traditional
cotton seamed belt.
We designed the seamless belt consisting of a unique
textile composite structure: two ply woven fabric
at the
external pasting surface and non-woven synthetic mat
with longitudinal reinforcing fabric at the internal
surface.
We then selected the most suitable raw materials,
and have developed and perfected an appropriate manufacturing
process to build a reliable production capacity to
meet pasting process engineers' most strict requirements.
A unique composite was so created by combining a textile
cotton material which is smooth and absorbent with
reinforcing fabrics (able to give the requested tensile
strength and controlled elongation) by a synthetic
non-woven mat (flexible and elastic).
The resulting composite structure depends on the yarns'
physical and chemical composition. |
GW:
And the advantages?
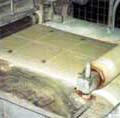
|
GT: Well, that's
obvious really. Belts come out "endless" from
the weaving looms and need no further seam or splice,
so no further joining or gluing is necessary.
The belt, which is made of cotton and synthetic fibres,
has the same strength in all its points and the well-known
"seam break zone" no longer exists. The belt
has the same thickness (about 9mm) and surface smoothness
throughout its circumference and that means a better
pasting and an improved distribution on battery grids.
Water absorption is uniform in every point of the belt
since no glue is used for seam purposes.
The belt runs straight on the pasting machine and does
not move towards one side or the other because it is
perfectly cylindrical. I.T.B. seamless belts are heat-set
at high temperature under a remarkable stretching load.
Their dimensional stability is therefore excellent throughout
their whole life. Length and width do not change even
under heavy working conditions, so the belt can work
very taut, but in no case do they create slipping under
heavy working machine rolls. I.T.B. belts are also protected
against abrasion by means of a patented material which
we have specially developed for this.
The result of all the above is the that belt lifetime
proved to be three to four times as much as the traditional
spliced belts. |
GW:
Regarding close tolerance plates, can you give typical
values on weight thickness and pasted weight and can
you compare old belt pasters with manual hopper control
versus more recent belt pasters with traditional cotton
belts or seamless belts? |
GT: As far as
close tolerance and thickness of the plates, this depends
on the manufactures. Most plates that are run on an
automotive paster are from 0.95 to 1.10mm thickness
with a ±0.05 to ±0.10mm tolerance.
Old belt pasters with manual hopper roll control and
traditional seamed cotton belts have pasted weight tolerance
of ±7 grams per plate. Modern pasters from MAC
(USA) and SOVEMA (Italy), with improved hopper control
and equipped with I.T.B. seamless belts can achieve
paste weight control of less than ±3 grams and
minimise paste waste. |
GW:
There's quite a difference on the price of your belts
compared to ordinary cotton isn't there?
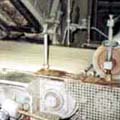
|
GT: The cost
of a traditional cotton belt for an automotive paster
is about US$90 while the equivalent I.T.B. seamless
belt is US$300. The enormous price difference has been
a shock for many buyers since our first commercial offer
in 1981, but a quick calculation may show how the extra
cost of seamless belt can be repaid by (i) less down
time, (ii) saving of paste through better weight tolerances
and (iii) much longer life time.
For example, a battery manufacturer producing one million
SLI batteries of various sizes needs 68 million plates,
i.e. 34 million panels (double plates). Using traditional
cotton belts, the manufacturer may need over 70 belts
while using I.T.B. seamless belts they may need only
30. There is an initial extra cost of seamless belts.
However, the pasting line down time for replacing the
belt is 30 times per year with seamless belts and 70
times with cotton belts, so there is a saving of about
40 hours per year in down time.
The correct use of a seamless pasting belt as well as
good operation and a good paster maintenance programme
can save tens of thousands of dollars in reduced paste
waste, energy and health care cost. It has been estimated
at a saving of US$60,000 a year with only 3 grmas of
paste saved per plate.
Another evident saving of paste is noticed when comparing
traditional seamed cotton belts with I.T.B. seamless
ones. For a battery manufacturer producing one million
SLI batteries per year and the hypothesis that 1 panel
using every 16 can be overpasted in the last third of
the cotton belt life time (because of the wearing of
the seaming zone), you have about one million panels
overpasted. If the overpasting is 3 or 4 grams per panel,
the manufacturer loses 3 to 4 tons of active material
per year.
Longer life time of I.T.B. seamless pasting belts is
today a proven fact all around the world, as they are
used by over 240 battery plants in 82 countries. The
life time of seamless belts proved to be at least 3
times that of the traditional cotton belts with a good
average of 1.1 million panels pasted per belt. In 1995
I.T.B. belts helped the battery industry to produce
over 140 million SLI batteries around the world. |
GW:
It's hard to argue with that. So what belts are there
on offer? |
GT: Battery manufacturers
can choose among several producers of traditional seamed
cotton belts or I.T.B. seamless ones. Seamless belts
can be offered in any size with no actual limits in
length or in width. |
GW:
So how do you get the best out of your belts?
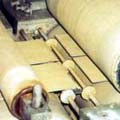
|
GT: There
are a few points you have to observe:
- The Paste
Belt pasting machines operate best with crunchy
paste because it has excellent cohesion to itself
and it will not penetrate the belt. This assures
longer belt life. The crunch of the paste is increased
by: (a) increasing the acid addition - increasing
the specific gravity (b) decreasing the speed of
the mixer. When the paste coming from the mixer
is too hot - over 38° C (100° F) - the moisture
in the paste will evaporate and change the consistency
of the paste. This can affect the operation of the
machine as well as the performance and life of the
belt. To facilitate a good machine operation, it
is also recommended that the paste be about 18 to
22 reading on a globe penetrometer. If paste sticks
to the belt, tighten the squeeze roller to remove
more moisture from the belt. If paste sticking or
pulling persists, the paste is too wet or the belt
is too old and saturated with hard oxide and must
be replaced
- The squeeze roll
The squeeze roll is used to squeeze water out of
the belt. It also presses the belt against the drive
roll to avoid belt slippage and to aid in belt guiding.
It is ideal to have sufficient moisture in the paste
to provide a flow of water out of the belt. If the
squeeze roll is adjusted too tight because of stiff
paste, the belt may stretch excessively. Also, stiff
paste will not stick well to the grids. Again, use
paste and a cut-off wire when necessary.
- Belt cleaning
For good plates and long belt life, the belt must
be cleaned and flushed until clean water comes out
of it at the squeeze roller. Also, inject water
to the underside of the belt next to the rollers.
This water will be forced through the belt by the
squeeze roll and flush out the paste and oxide.
If residual paste in the mixture is allowed to harden,
it will damage the water absorbency of the belt
and it will also crack the belt fibres. Therefore,
keep the belt wet all times when the machine is
not in use.
- Belt life-time
Under good operating conditions an I.T.B. belt can
easily paste over 1.1m panels. Once a belt is saturated
with paste and the surface is too smooth and too
hard, little can be done except install a new belt.
When the top surface of a belt has worn smooth,
the oxide will tend to stick even when the moisture
content in the belt is correct. In this case belt
life can be extended considerably by placing a steel
cut-off wire (piano wire) diagonally across the
belt surface to separate the plates. When the pasting
belt is new, the use of the piano wire is not recommended.
If paste begins to pull from the panels, the wire
can be added. The "plate finishing rolls"
(located at the exit end of the paster) wrapped
with a cheese cloth or tobacco cloth will absorb
moisture from the pasted panels to the upper and
lower pasted panel surfaces. This extra added surface
texture has been found to add to the plate's initial
cranking performance. Also, when the belt pulls
paste, look for the following:
a) belt or paste is too wet
b) belt scraper is not cleaning the belt
c) squeeze roller is not tight enough to remove
enough water from the belt
d) belt is saturated with paste and has lost the
property to absorb water
|
GW:
Finally, what's the future of pasting. What is your
opinion on the survival of belt pasting? |
GT: I believe
that belt pasters will be used for many years to come
for it is a good, low overhead way of making lead battery
plates. In addition, the continuous improvements in
seamless pasting belts allow battery makers to produce
plates with low cost, good flexibility and close tolerances.
|